Cutting Tool
Critical Factors When Choosing A Cutting Tool
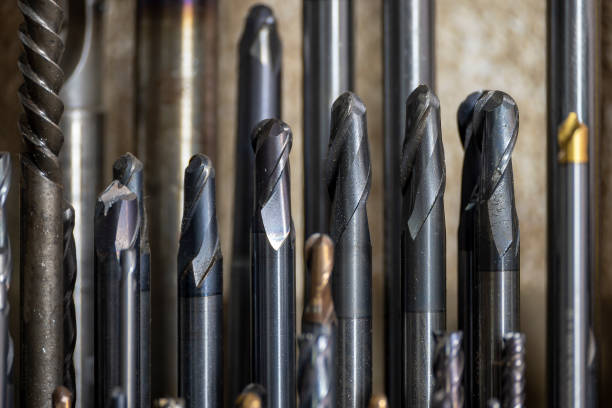
If you are choosing a tool for cutting be sure to take into consideration its material properties and what it can do to cut an individual material. The K-factor will be discussed, chemical stability and the cutting angles of the sides as well as other aspects.
A cutting tool that is as good similar to pencil grinders and straight grinder tools can save you time and money while ensuring quality results. Listed below are some essential aspects to consider when choosing a cutting tool. Check with your machine shop for specific equipment if you're not sure what you require. When you aim to find out more details about tools, you have to sneak a peek at https://www.sundicuttingtools.com/products/full-solid-cbn-inserts/ site.
1. Materials Properties
The properties of the material used in cutting tools form the fundamental specifications for the effectiveness of different machining processes. These tools, unlike knives, need to stand temperatures of over 100°C without loosing their cutting edge. Additionally, they must be resistant to abrasion, adhesion as well as thermal conductivity.
These aspects are vital to the optimum performance of cutting instruments. We will now discuss specific properties of the material to help understand the use of as well as the lifespan of cutting equipment.
The process of production is based on the lifespan and the speed at which it operates. The life of the cutting tool is influenced by many factors including the rate of feed, geometry of the tool as well as wear of the tool. These variables can affect the tool's longevity and productivity.
A good cutting tool will last for many hundreds of thousands of cuts. Its life is determined by the ability of cutting different substances at different speeds. In addition to cutting speeds the cutting tool must feature a high resistance to wear. This is why taking note of the feeding speed and cutting rate prior to purchasing a new tool is essential.
2. K Factor
The K-factor for cutting tools determines the appearance of the edges. The diameter of the cutting edge is the result of many factors, including the material, the machining process, and the type of material used.
But, it's usually measured based on cutting rates which are about 35 milliseconds. Fig. illustrates the area of monitoring at the cutting edge. 1. The size of the Sa and Sy affect the force load and heat load.
To determine the K-factor of cutting tools, a tool is made of metal as well as alumina and the abrasive. Its K factor is affected by the length of the contact and the inclination of g. As the rake angle grows, the objective roughness of the function increases.
The more intricate the material, the more complex the roughness objective function. A higher K factor means the cutting tool is not operating properly.
3. Chemical Stability
CBN-based cutting tools are made of a complex material. They are also high-temperature resistant and exhibit outstanding thermal stability. They can be classified as low-c-BN and high-c BN. Low-cBN tools do not contain CBN, whereas the high-cBN ones contain between 75 and 95 percent boron-nitride and metallic binder.
While greasy oils are the most widely used cutting fluids, their additional features are merely modest. They're also costly and produce a lot of smoke that makes the oils unfit for production in modern times. But, they can be formulated to be low-viscosity by mixing mineral oils with EP additives. The combination of mineral oils and EP additives can provide excellent lubricity as well as a greater tool's lifespan.
4. Side Cutting Edge Angle
The angle at which the back rake is determined determines a cutting edge of the tool's cut side angle. The angle is measured from the edge of the cutting tool and the plane of perpendicularity. In the event that it slopes down, the tip is positive and if it's upwards, the angle will be negative.
The back rake typically is between 5 and 15 degrees. This angle is vital to consider when planning and manufacturing a tool.
The rake angle of a cutting tool is determined by the tool's face as well as a line that runs parallel to the tool's base. The rake angle is formed by the face of the tool and a line parallel to its base.
Positive rake angles reduce the heat-conduction capability of the tool and the strength that the edge. So, positive rake angles are better for hard metals as well as tough alloys. positive rake angles are more suitable for soft and brittle metals.
5. High Yield Strength at Operating Temperature
High yield strength is one of the most popular features associated with HSS tools. This kind of tool is designed to be loaded to its maximum yield strength. But, it could result in severe wear to the adhesive surface.
The wear can be further accelerated by cutting chemically aggressive materials. Along with the extreme wear on the adhesive, HSS cutting tools are susceptible to sharpening their edges due to excessive friction. This article explains the causes that affect yield of cutting equipment.
A tool's operating temperature is a major factor in determining the amount of heat generated by the tool during cutting. The maximum temperature of a cutting tool is increased with increasing speed of cutting because the temperature of the work material is affected by the quantity of heat that is flowing through the cutting tool.
The effect of this can be seen most clearly with intermittent cutting. The temperature of the operating area can play a significant role in the lifespan of a tool and its quality. It must be able of cutting at a particular temperature to improve its life expectancy and to reduce the production of heat.
6. Tool Material
The hardness at high temperatures of a tool material determines its capacity to stand up to heat, prevent plastic deformation, and maintain toughness at extremely high temperatures. It also affects its wear resistance.
The more stable thermally the material used for tooling is, the better its capacity to endure a cutting process. Its temperature will be reduced while cutting if it's got a better thermal conductivity. The selection of a material which can be able to withstand cutting at high speeds is crucial.
For industrial use the cutting tools is essential. It determines the quantity of material that is removed, the surface finish, the tolerance, and the cost for the maker.
Last Words
Manufacturers can reduce scrap, improve production rates, and enhance part quality through selecting the right tooling material. This ensures the longevity of their operation. To choose the right materials for cutting tools, a company should first look at the specific specifications of their cutting tools.